Methods and Construction
Casting
Initial Casting
First the medallion models were 3D printed and were freely placed in the sand without the match plate. The runners were then made by hand and without a match plate which took longer. After the aluminum was heated in the furnace, and the crucible filled, the aluminum was poured. Once cooled, the excess aluminum was cut off using the band saw and ground with a sander.
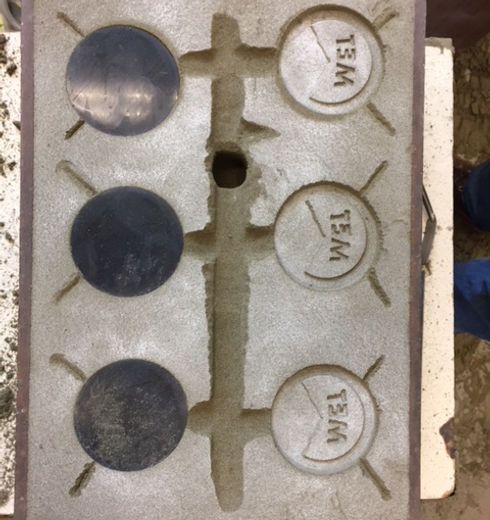
Creation of the Match Plate
Half inch plywood was purchased for use of the base. The runners were 3D printed from PLA in two sections to fit within the limits of the printer. Epoxy adhered each of the parts to create the match plate.

The Pour
Aluminum fills the mold by being poured through the sprue.

All Casted Medallions
Left to right: first casted design, updated design, machined medallion as mold.

Methods and Construction
CNC
From 3.5 inch Round
The horizontal band saw with a stop was bolted to the table to cut small disks from a 3.5” aluminum round bar.

Turning
CNC lathe already had programs to face and chamfer embedded into the machine, thus only imputes needed to be defined such as the depth of cut and the zeros.

CNC Mill
Final Operation
Face with a 1 inch end-mill, rough with a 3/16 end-mill, finish with a 1/4 inch ball end-mill.

Finished Medallion
The medallion sits completed in the custom 3-jaw chuck.
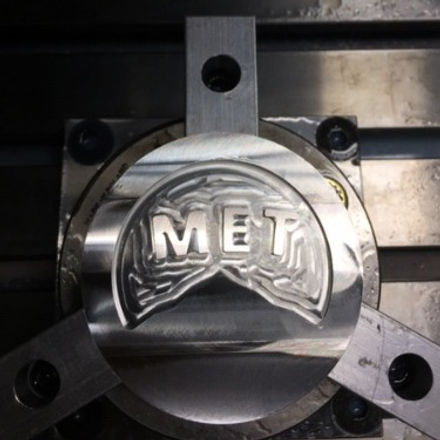
